Warum Schrumpftechnik nachhaltiger ist
Die Werkzeugspannung unter Nachhaltigkeitsgesichtspunkten
Wenn Werkzeuge sicher gespannt werden müssen und dabei auch ein guter Rundlauf gewährleistet sein soll, führt bei den Spannmitteln kein Weg am Schrumpfen vorbei. Bei der Auswahl zwischen den verschiedenen Verfahren spielen meist technische Anforderungen die entscheidende Rolle. Doch kann man inzwischen in diese Entscheidung auch Nachhaltigkeitsgesichtspunkte mit einbeziehen, insbesondere bei der modernen Schrumpftechnik.
Schrumpffutter, Spannzangenfutter und auch Hydrodehnspannfuttern haben in der Anwendungstechnik alle ihre Berechtigung. Wenn man die Nachhaltigkeit mit einbezieht, ergeben sich jedoch deutliche Unterschiede sowie neue Erkenntnisse, die den früheren Stand der Technik deutlich umkrempeln und auf die Unterhaltskosten, also „Cost of ownership“ einen interessanten Einfluss haben. Die Nachhaltigkeit kann also plötzlich als zusätzliches Entscheidungskriterium dienen.
Lebensdauer ist ein entscheidender Punkt für Nachhaltigkeit
Ein namhafter Hersteller von Hydrodehnspannfuttern hat für sich ermittelt, dass Hydrodehnspannfutter mindestens zehnmal länger halten als Schrumpffutter (bei denen die alte Schrumpftechnik zur Anwendung kam). Hydrodehnspannfutter eignen sich laut diesem Hersteller für die Wiederaufbereitung. Beim Service werden die Einbauteile ersetzt und das Hydrauliköl neu aufgefüllt. Danach ist das Hydrodehnfutter bereit für eine zweite Lebenszeit. Echte Nachhaltigkeit ist das jedoch nicht, denn der Reparaturaufwand ist erheblich und verbraucht jede Menge Ressourcen.
Mit den intelligenten Schrumpfgeräten von Diebold erfolgt der Schrumpfvorgang durch schonendes Erhitzen sowie dem gleichmäßigen Abkühlen der Aufnahme im TubeChiller® mittels einer Kühlflüssigkeit. Dabei wird der Wasserspiegel angehoben, wodurch das Schrumpffutter ringförmig umspült wird. Würde das Schrumpffutter dagegen „geduscht“, ist die Gefahr groß, dass sich der Fräser „verbiegt“. Diese Formänderung erfolgt zwar nur im mµ-Bereich, aber auch diese Abweichung ist auf keinen Fall erwünscht und wird durch die Flüssigkeits-Hebetechnik ausgeschlossen. Der Markterfolg der neuen Schrumpfgeräte von Diebold zeigt deutlich, dass die Anwender sich genau für diese Technik entscheiden.
Der doppelt bis dreimal so hohe Preis eines hydraulischen Futters macht sich heute also nicht mehr bezahlt, weil die Investition in ein vollautomatisches und intelligentes Schrumpfgerät der Top-Linie, das mit allen Optionen ausgestattet ist, ab dem 46. Hydrodehnspannfutter bereits amortisiert ist. Wenn man bedenkt, dass moderne Maschinen heute Werkzeugmagazine mit mehreren Hundert Werkzeugaufnahmen haben, geht diese Rechnung schon sehr schnell auf und multipliziert sich mehrfach über die ganze Lebensdauer einer Maschine.
Bedienung leicht gemacht durch OneTouch®
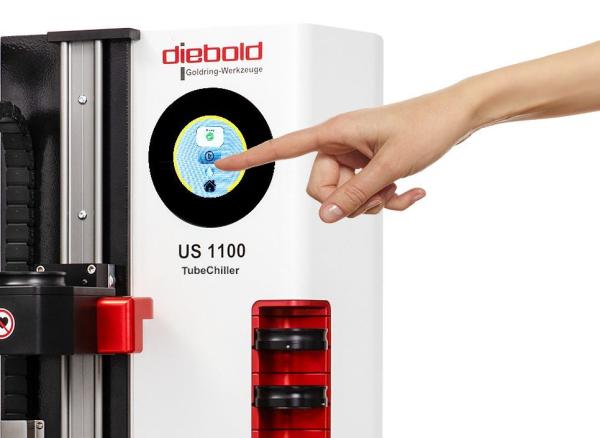
OneTouch® ist die neue Bedienungsform der Diebold Schrumpfgeräte für intelligentes Schrumpfen. Vor allem junge Menschen lieben diese einfache und unproblematische Handhabung, denn so wollen sie zukünftig arbeiten und mit Technologie versorgt werden. Mit einem Touch wird der vollautomatische Schrumpf-Prozess gestartet. Mit kleinstem Energieeintrag wird die Temperatur an der Oberfläche des Schrumpffutters ständig überwacht und geregelt. Wenn sich das Werkzeug beim Schrumpfprozess nicht sofort lösen oder einsetzen lässt, dann wird automatisch über eine digitale Rampe mit minimalstem Energieeintrag nachgeheizt, bis der Schrumpfprozess erledigt ist. Ein Verändern der Parameter oder jegliche händische Eingabe ist dabei nicht notwendig. Alle möglichen Bedienungsfehler sind damit ausgeschlossen.
Schrumpfgeräte sind keine Stromfresser
Intelligentes Schrumpfen erfordert nur die minimale Energieabgabe des Hochfrequenzgenerators, denn die stetige Überwachung der Temperatur regelt den Energieeintrag intelligent, was den Energieverbrauch auf ein Minimum senkt. Auch die Abkühlzeit wird dadurch reduziert, weil die Aufnahmen nur auf eine minimale, für den Schrumpfprozess nötige Temperatur erhitzt werden. Zum Kühlen wird überhaupt keine Fremdenergie mehr benötigt, wie es bisher bei Geräten mit wasserdurchfluteten Kühlglocken der Fall war, da hier die Kühlflüssigkeit ständig durch ein stromfressendes Kühlgerät gepumpt werden muss. Beim TubeChiller® von Diebold wird zum Abkühlen der Schrumpffutter der Wasserspiegel im Gerät lediglich mit der vorhandenen Druckluft aus dem Firmennetz angehoben, Umgebungs-Luft strömt nach und kühlt das Kühlwasser nach jedem Kühlvorgang wieder ab. Dies alles passiert dadurch fast „kostenlos“ und ohne zusätzlichen Energieaufwand.
Die Nachhaltigkeit in der Produktion gewinnt zunehmend an Bedeutung und man kann mit intelligenter Schrumpftechnik leicht nachweisen, wie man seinen CO2-Fußabdruck reduziert.
Bei der Wirtschaftlichkeitsrechnung zwischen Schrumpf- und Hydrodehnspanntechnik spielt neben der Lebensdauer der Spannfutter und dem Energiebedarf der Geräte auch der Faktor Zeit eine Rolle. Mit intelligenter Schrumpftechnik können in fünf Minuten auch fünf Schrumpfzyklen erledigt werden. Der Hersteller von Hydrodehnspannfuttern gibt eine Wechselzeit von maximal zwei Minuten an. Also haben Dehnspannfutter hier keinen Zeitvorteil mehr zu bieten.
Einfach und sicher
Intelligente Schrumpfgeräte mit automatischer Kühlung stellen keine potenzielle Gefahrenquelle da. Die Sicherheitsingenieure verlangen heute diese Technik, dass alle Prozesse überwacht sind, Fehlbedienungen ausgeschlossen sind und ein Bediener sich nicht mehr die Finger an einem heißen Spannfutter verbrennen könnte.
Das Fazit des Vergleichs fällt eindeutig aus: Schrumpftechnik ist energiesparend, langlebig und problemlos in der Fertigung anzuwenden. Es gibt keine Argumente mehr, die dagegensprechen würden, Schrumpftechnik in der Zerspanung einzusetzen.
Im Gegenteil, man kann die vielen Vorteile der Schrumpftechnik voll ausschöpfen:
Hohe Rundlaufgenauigkeit
Extreme Spannkraft
Einteiliger Aufbau
Keine beweglichen Bauteile
Geringe Störkonturen durch schlanke Bauform
Hohe Drehzahlen für Hochgeschwindigkeitsfräsen
Spiegelnde Oberflächen durch hohe Genauigkeit
Kein Verschleiß, dadurch kein Aufwand für Reparaturen oder Instandsetzungen
Äußerst lange Lebensdauer
Wer nachhaltig und verantwortungsbewusst in der Fertigung unterwegs sein will, ist mit intelligenter Schrumpftechnik auf der Höhe der Zeit sowie der Wirtschaftlichkeit. Nicht zuletzt wurde diese Technik von Diebold zur Messe AMB 2022 durch das Votum der Anwender bestätigt und mit dem MM Award ausgezeichnet.
Helmut Diebold GmbH & Co.
Die Helmut Diebold GmbH & Co. KG ist mit seiner intelligenten Schrumpftechnik zum technologischen Weltmarktführer geworden. Als international führender Anbieter von Werkzeugaufnahmen für die Hochgeschwindigkeitsbearbeitung ist die Schrumpftechnik ein wichtiger Anteil für die Kunden aus der Mikrobearbeitung, der Medizintechnik, der Optik, der Feinmechanik oder der Uhrenindustrie. Das Familienunternehmen betreibt intensive Entwicklungen und besitzt viele Patente für verschiedenste Anwendungstechniken. Mit seinen Innovationen setzt das Unternehmen Standards in der Spanntechnik. Diebold beschäftigt an seinem einzigen Standort in Jungingen 120 Mitarbeiter und betreibt intensive Nachwuchs-Ausbildung. Über 70 % der Mitarbeiter haben ihre Ausbildung im Unternehmen gemacht.