Katapultstart in die Vollautomation
Technologieübergreifend bei höchster Präzision
Die weltweit tätige Schweizer SFS-Gruppe beliefert zahlreiche Branchen mit anspruchsvollen Bauteilen und Baugruppen. Für die Herstellung von Spritzgießformen setzt das Unternehmen aus Qualitätsgründen auf den eigenen Formenbau in Korneuburg (Österreich). Hier wurde Anfang 2022 eine integrierte Fertigungslinie mit Fräs- und Senkerodieranlagen, Teilereinigung und hochpräziser Vermessung in Betrieb genommen. Ein Gespräch mit dem Abteilungsleiter über die dabei gemachten Erfahrungen.
„Die SFS Gruppe beliefert Hightechbranchen wie Automobilhersteller, die Elektronikindustrie, die Luft- und Raumfahrt, die Bauindustrie oder die Medizintechnik mit Präzisionsteilen oder kompletten Baugruppen aus Kunststoff und/oder Metallen“, erläutert Heinrich Ruckenbauer, Leiter Werkzeugbau der SFS in Korneuburg (Österreich). Seine Abteilung stellt schwerpunktmäßig komplexe Spritzgießwerkzeuge für die Werke der Gruppe in Österreich und Ungarn her. Die produzierten Kunststoffteile müssen höchste Ansprüche erfüllen.
Oft geht es dabei um Sicherheitsfunktionen wie beispielsweise bei Bremsen oder Gurtstraffern im Automobil. Bei Komponenten für das Interieur von Fahrzeugen wie Türbetätigungshebeln kommt es zudem auf höchste Oberflächenqualität an. Fehler könnten – beispielsweise beim Versagen von Sicherheitsteilen – enorme Konsequenzen nach sich ziehen. Entsprechend hoch sind daher die Anforderungen an die Qualität der von seiner Abteilung hergestellten Werkzeuge, denn jeder Fehler im Werkzeug würde sich unweigerlich auch im Produkt abbilden.
Zusätzliche Anforderungen
„Über die reine Geometrietreue der erzeugten Spritzgussteile hinaus sind für uns außerdem noch Kosten- und Technologieaspekte ausschlaggebend“, ergänzt H. Ruckenbauer. Wie alle Zulieferer muss sich auch SFS in einem ständigen harten Preiswettbewerb gegen Anbieter mit teils erheblich niedrigeren Standort- und Personalkosten behaupten. Da die Werkzeuge beim Spritzgießen ein wichtiger Kostenfaktor sind, muss seine Abteilung ständig nach Möglichkeiten zur Kostensenkung Ausschau halten. Das erforderte zwingend eine Erhöhung der Produktivität durch Automatisierung. Gesucht wurde daher eine Lösung, die einen vollautomatischen, technologieübergreifenden Betrieb mit mindestens 5.000 Einsatzstunden pro Jahr ermöglichen sollte.
Ein weiterer Gesichtspunkt waren höhere Anforderungen an die Bandbreite der bearbeitbaren Werkstoffe. Dies gilt insbesondere für Werkzeugbestandteile aus Hartmetall. Stähle werden durch moderne, bis zu 75 % mit Mineralstoffen gefüllte Kunststoffe oft zu schnell verschlissen. Hartmetalle ermöglichen in solchen Fällen deutlich höhere Standzeiten.
Komplettumbau der Formherstellung
„Wir wollten deshalb unsere bisherige Ausstattung mit Einzelmaschinen durch eine moderne, voll automatisierte Fertigungslinie ersetzen, mit der alle bei uns vorkommenden Aufgabenstellungen einschließlich des Vorrichtungsbaus durchgeführt werden konnten“, sagt H. Ruckenbauer. Dabei stand höchste Präzision der zu beschaffenden Maschinen bis hin zur Herstellung von Meisterteilen ebenso im Vordergrund wie die Integration Technologien Fräsen, Senkerodieren, Reinigen der Werkstücke sowie ihre Vermessung über eine Automation. Nach gründlicher Vorklärung habe man sich für die von Röders in Soltau vorgeschlagene Lösung entschieden. Deren Fräsmaschinen erreichen höchste Genauigkeit und können auch Hartmetall bearbeiten.
In der neuen Linie werden neben formgebenden Werkzeugbestandteilen auch Aufnahmen und Lehren sowie Meisterteile hergestellt. Die einzelnen Anlagen sind nebeneinander angeordnet und werden von dem sehr schmal bauenden Handling RCF 150 von Röders auf einer gut 11m langen Linearschiene bedient. Angebunden sind eine fünfachsige Röders-Fräsmaschine RXP 501 DS, eine dreiachsige Röders RXP 501, eine Senkerodieranlage Sodick AG 60 L, eine automatische Reinigungsstation Erowa RoboSpa sowie ein Koordinatenmessgerät Hexagon TIGO SF.
An der den Maschinen gegenüberliegenden Seite befinden sich Regale mit Fräswerkzeugen, Robotergreifern, Paletten von Erowa für Elektroden und Werkstücke in drei verschiedenen Abmessungen. Beschickung bzw. Austausch der bis zu 150kg schweren Werkstücke erfolgen über eine Beladestation. Verwaltet wird die gesamte Linie über das ebenfalls von Röders entwickelte, eigene Jobmanagementsystem RMSMain, das die NC-Programme vom CAM-System (Visi) per automatischem Datenimport erhält. Hervorgehoben werden kann bei diesem Handling insbesondere die Kompaktheit, aufgrund der speziellen Armkonstruktion mit Rotationsgelenken kommt das Handling mit einer Breite von lediglich 1,5m aus. Aufgrund des begrenzten Platzes in der Werkstatt war dies ein nicht zu unterschätzenden Pluspunkt für die Anlage von Röders, so der Werkzeugbauleiter.
Produktionshochlauf innerhalb von vier Wochen
„Vor der Entscheidung gab es gutgemeinte Warnungen, dass es bis zu einem halben Jahr dauern könne, bis wir mit dem System produzieren können“, schmunzelt H. Ruckenbauer. Die Steuerungen wie auch das Jobmanagement waren jedoch so bedienerfreundlich und die Schulung so effektiv, dass erste Einzelteile schon zwei Wochen nach Inbetriebnahme gefräst werden konnten. Bis zum Anlaufen des vollautomatischen Betriebs dauerte es nur zwei weitere Wochen. Danach konnte die Linie dank kompetenter telefonischer Unterstützung durch Röders schnell auf die anvisierten 400 Einsatzstunden pro Monat hochgefahren werden. Hilfreich dabei war sicherlich auch, dass aufgrund der Lieferung von Fräsmaschinen mit Steuerung und Handling inkl. Jobmanager vom Systemverantwortlichen Röders nur wenige Schnittstellen – zu den angebundenen weiteren Maschinen – vorhanden waren, die ja häufig für Störungen und Verzögerungen sorgen, so H. Ruckenbauer.
Entscheidende Rolle der Belegschaft
„Bei einem solchen Projekt sind die Mitarbeiter entscheidend. Ohne ihre Akzeptanz und ihr aktives Engagement wäre der Erfolg des Projekts nicht so durchschlagend gewesen“, erinnert sich H. Ruckenbauer. Die in diesem Bereich tätige Mannschaft musste nicht nur die neue Steuerung kennenlernen, sondern auch ihre Arbeitsweise umstellen. Früher führten sie nur bestimmte Teile der Prozesskette wie z.B. CAM-Programmieren, Fräsen oder Erodieren aus. Jetzt übernehmen sie dagegen die Verantwortung für die gesamte Bearbeitung der ihnen anvertrauten Werkstücke von der CAM-Programmierung bis zum abschließenden Messdurchlauf.
In diesem Zusammenhang mussten sie sich auch von liebgewonnenen Gewohnheiten verabschieden. Wenn der Mitarbeiter früher mit dem NC-Programm nicht zum gewünschten Ergebnis kam, wurden schon mal „auf die Schnelle“ einige Sequenzen direkt an der Maschine modifiziert. Das Teil war dann zwar „i.O.“, aber es gab keine Rückführung ins CAM-Archiv und somit keine Reproduzierbarkeit des Fertigungsprozesses im Falle einer erneuten Fertigung des entsprechenden Bauteils. Inzwischen hätten alle im Team akzeptiert, dass solche Modifikationen nicht mehr händisch durchgeführt werden, sondern grundsätzlich zuerst am CAM-System vorzunehmen sind. Von der Zelle werden diese dabei optimal unterstützt, da alle nötigen Arbeitsschritte wie das Reinigen und Waschen stets ohne manuelles Zutun erfolgen.
Mit Ergebnissen „hoch zufrieden“
„Nach inzwischen gut einem Jahr Betrieb kann ich sagen, dass wir mit den Ergebnissen des Projekts hoch zufrieden sind“, bilanziert H. Ruckenbauer. Bei der Genauigkeit habe man einen geradezu extremen Sprung nach vorne gemacht. Wo früher über hundertstel Millimeter gesprochen wurde, werde heute über Mikrometer diskutiert. An den Teilen werde heute vierstellig nach dem Komma gemessen, selbst bei solchen, die auf der Röders RXP 501 DS fünfachsig gefräst wurden. Auch sei die Reklamationsquote seit Verwendung der neuen Linie um über 50% zurückgegangen.
Die Genauigkeit der Linie werde heute routinemäßig genau überwacht, alle drei Tage laufe auf der Anlage eine Überprüfung der Kalibrierung als eigener Job. Dabei habe man auch interessante Zusammenhänge feststellen können. So seien die Toleranzen beim automatischen Palettenwechsel durch den Roboter signifikant enger als früher beim händischen Austausch. CBN-Kopierfräser erwiesen sich bei der µm-genauen Bearbeitung von Freiformflächen zudem als genauer als solche aus Hartmetall.
Auch bei der Produktivität habe es einen erheblichen Sprung von rund 30 % bei gleicher Mannschaftsstärke gegeben. Besonders hervorzuheben sei aus seiner Sicht auch die hohe Servicebereitschaft des Herstellers. Im Vergleich zur Situation vor Einführung dieser automatisierten Fertigungslinie erlebe man jetzt eine gewaltige Verbesserung in allen Bereichen.
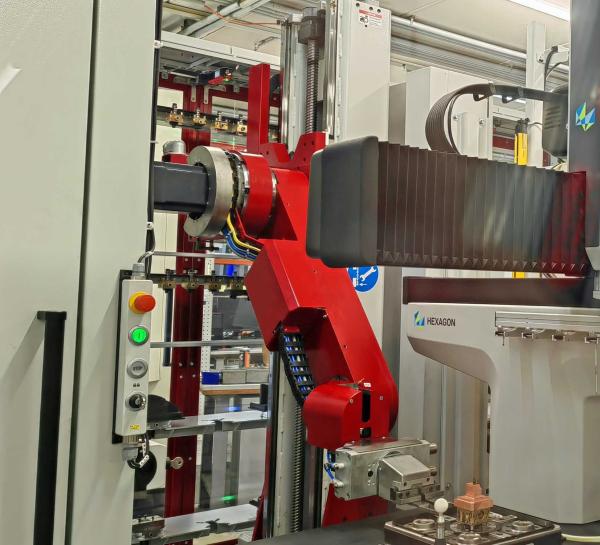
In vielen Werkstätten ist Platz Mangelware. Dem kommt der flexibel einsetzbare Handlingroboter RCF 150 mit seiner schmalen Silhouette entgegen. Mit nur einem Meter „Schulterbreite“ und hochdynamischen Antrieben bewegt er sich auf seiner Linearschiene zwischen den Maschinen und der mit lediglich 50 cm Breite ebenfalls sehr schlank bauenden Regalreihe. Dennoch reicht er mit seinem Arm auch bei maximaler Beladung (150 kg) um bis zu 1750 mm in die einzelnen Maschinenräume hinein. Mit diesem platzsparenden Gerät lassen sich sehr kompakte Automationslinien realisieren.
Das dank modularer Bauweise schnell installierbare System ist in Stufen erweiterbar und transportiert sowohl Werkstücke als auch Werkzeuge. Mit seinem Greiferbahnhof sind jederzeit Greiferwechsel möglich. Die maximalen Werkstückabmessungen liegen bei 320 x 320 mm. Optional ist auch Chipidentifikation verfügbar. Die Ansteuerung erfolgt über die Jobmanagementsoftware auf dem Leitrechner, bei Einmaschinenbedienung kann das aber auch die Maschinensteuerung übernehmen.
Röders GmbH
Röders GmbH
Gottlieb-Daimler-Str. 6
29614 Soltau
Tel. +49 5191-603-43
Fax +49 5191-603-38
E-Mail info@roeders.de